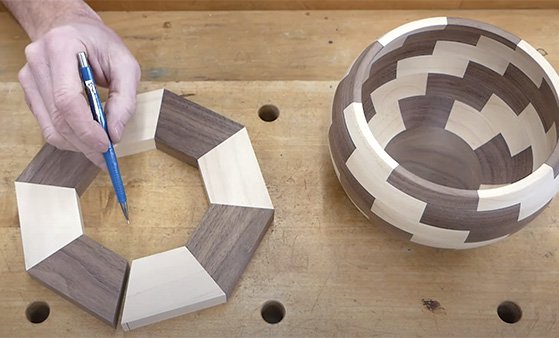
Philip Moulthrop began turning wooden in 1979. He learned his craft from his dad, Ed Moulthrop. He cuts the green parts of trees in the southeastern region using a chain saw and a hand-forged lathe. He finishes the bowl by turning it on the lathe. This entire process can take anywhere from 4 months to 1 year. Once complete, the bowls are ready to be purchased or given as gifts.
Philip Moulthrop
Phillip Moulthrop Bowl is a beautiful red leopard maple vessel. For three generations, wood turning has been a family tradition. Philip Moulthrop and his family have made many bowls that are now part of the permanent collections at several museums and private collections. Here are some of their most renowned pieces. Continue reading to learn more about this talented artist.
Born in 1947, American artist Philip Moulthrop. In his 20s, he studied general arts and soon discovered a passion for woodworking. At the age of 16, he purchased his first machine and continued to improve his skills. He developed his techniques, producing beautiful turned vessels that attracted the attention of the art community and even the United States President. After his work had been recognized, he started selling his products at local craft shows and galleries. This earned him international recognition.
Matt Moulthrop
The Matt Moulthrop Bows are an excellent example of Georgia's rich woodturning traditions. The artist was born and raised in Atlanta. He received his BA from Georgia Tech and MBA from Georgia Tech. While he did spend a few years in the 9-to-5 industry, he never lost passion for turning wood. In fact, he received recognition nationally for his bowls. His works are on display at the ASU Art Museum as well the Carter Center and Racine Art Museum.
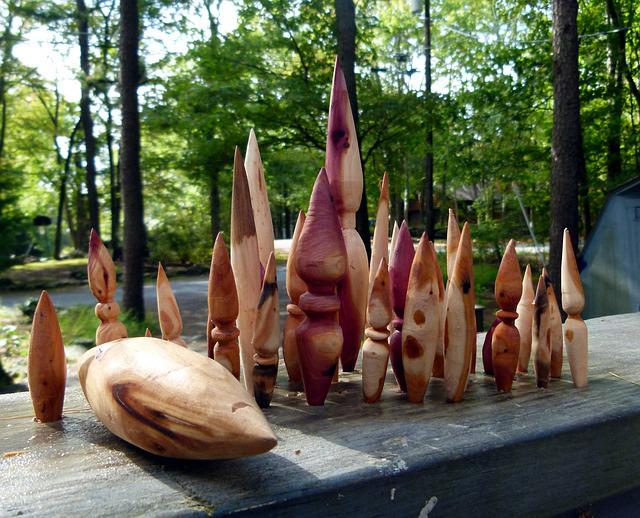
The Moulthrops have been recognized as world-class wood-turners, with works placed in prominent collections in the United States and abroad. Moulthrop's own pieces are held in the Renwick Gallery of the National Museum of American Art. Collectors from all over the globe have taken to heart his bowls. During a Smithsonian photo shoot he signed every photographer a copy of his family's book.
Ed Moulthrop
Moulthrop began making bowls in the 1970s. He soon received a scholarship from Princeton University to study architecture. Moulthrop left architecture after a year spent in Vietnam to learn woodturning. His large-scale turn bowls, which were internationally recognized, are now held in prestigious museums such as The White House Collection of American Crafts and Museum of Arts and Design. These bowls were made from domestic woods, and are polished to a clear shine.
This rare Ed Moulthrop box measures nine inches by fourteen inches. It is made from wild cherry. These wood bowls will be available for purchase at Gump's San Francisco. You can also see other Ed Moulthrop wooden bowls. It is a great way to see the work of the artisan. His work can also be found in a beautifully printed catalog. Although you can purchase his bowls at museums, it's better to visit his studio to actually see them in person.
The Eagle & Phenix Dam Series
This limited edition series is made with wood from the Eagle & Phenix Dam. They are handmade by Philip Moulthrop, local artists. They are available to bid during regular museum hours. Additionally, a portion will be offered for sale live.
The Moulthrop family has contributed to the growth of wood-turned bowls in Georgia. The museum proudly displays works by all three generations of the Moulthrop family, who have been turning bowls for more than five decades. These pieces are prized for their large sizes and smooth, polished surfaces. His mosaic bowl technique, which involves glueing thin branches to a shaped bowl with thin branches, is featured in the exhibit.
Matt Moulthrop’s work
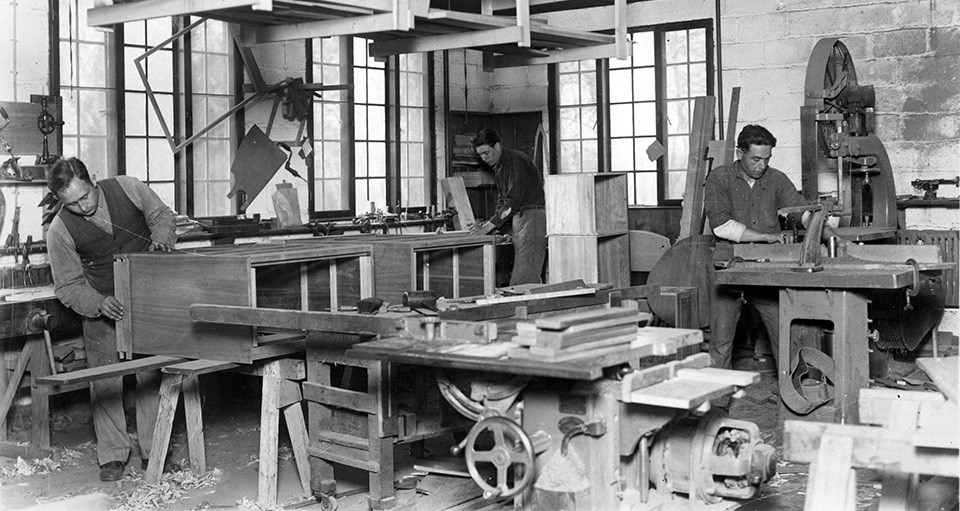
A son of Philip and Ed Moulthrop, Matt Moulthrop grew up around woodturning. He was taught by his father at an early age, and his passion for woodworking grew. Matt earned his BA at Georgia Tech and his MBA from Georgia Tech. After that, he turned his attention to woodworking as a profession. He is the third generation of woodworkers. His work is included in numerous art institutions, including ASU Art Museum and Carter Center. He is currently working on commemorative pieces for the Georgia Tech Alumni Association's 100th anniversary.
Georgia is not home for the wood he transforms. To find wood that is not common, he travels around the world. He works with tools and a hand-forged turning lathe to make unique pieces from trees from all around the world. Wood from exotic places, such as volcanoes or underwater forests, is used to make his pieces. If you love his work, make sure you check it out!
FAQ
What types of woods are best for furniture making?
Woods are classified according their hardness. Softwoods can be pine, fir or cedar. Because they are resistant, they can be used for outdoor furniture. You can find hardwoods like oak, maple, mahogany, teak, and others. They can't withstand the elements outside so they're best kept indoors.
Where can I find my woodworking tools?
There are many places that you can find all the information you need. You could shop at your local hardware store or go online to Amazon.com.
You might also consider flea markets and garage sale for any old furniture or other materials you could reuse.
What's the difference between a hobbyist and a professional woodworker?
Hobbyists are passionate about making things from wood, while professionals tend to be more focused on the quality and craftsmanship of their work. Hobbyists often take pride in the creations they make and often share them to family and friends. Professionals will spend hours researching designs and then begin to create a project. They will pay attention to every detail, from selecting the best materials to finishing the project perfectly.
What would be your first step in woodworking?
Start with softwoods such as pine and poplar. You will feel more comfortable with these softwoods, so you can move onto hardwood.
How much should a Woodworker Charge per Hour?
The hourly rate paid to a professional woodworker is dependent on many factors. These include skill level, availability, and location.
An hourly wage for skilled woodworkers is between $20 and $50.
A woodworker with less experience may be able to charge $10 an hour.
Statistics
- The U.S. Bureau of Labor Statistics (BLS) estimates that the number of jobs for woodworkers will decline by 4% between 2019 and 2029. (indeed.com)
- If your lumber isn't as dry as you would like when you purchase it (over 22% in Glen Huey's opinion…probably over 10-15% in my opinion), then it's a good idea to let it acclimate to your workshop for a couple of weeks. (woodandshop.com)
- Average lumber prices rose about 600 percent between April 2020 and May 2021. (familyhandyman.com)
- In 2014, there were just over 237,000 jobs for all woodworkers, with other wood product manufacturing employing 23 percent; wood kitchen cabinets and countertop manufacturing employing 21 percent. (theartcareerproject.com)
External Links
How To
How to stain hardwood
The process of staining wood involves the application of chemicals to the wood's surface, which causes it to change its color. This chemical reaction causes wood to turn from whiteish to brownish. Oak is the most commonly used wood for staining, but other woods can also be stained.
There are many options for applying stains to wood surfaces. Some methods include mixing the stain along with a solvent like turpentine and then applying the mixture to the wood by brushing or spraying. Others use a solution made up of water and dye, which is then applied directly onto the wood. The stain can be mixed with paints and varnishes to become part of the final coating.
Preparing the surface is the most important step in staining wooden surfaces. The wood must be thoroughly cleaned to remove all grease and dirt. Sanding the wood removes scratches and imperfections. Next, you need to decide which stain you want. There are two basic kinds of stains: penetrating stains and non-penetrating stains. Penetrating stains penetrate deeper into the wood than non-penetrating ones, making them ideal for dark colors such as mahogany. Light colors such as maple work well with non-penetrating stain.
After choosing the type and application method you prefer, gather your tools. A paintbrush works well for applying stains because it allows you to spread the liquid evenly across the surface. After you're done painting, make sure to have some rags handy to remove any excess stain. If you are planning to mix your stain, ensure you have enough containers for each component.
After you have prepared the materials, you can clean the area where you want to stain the wood. To remove dirt and dust, use warm water and soap. Wipe down all furniture pieces with a dampened cloth and clean water. You should remove any debris, especially if your plan is to stain darker wood.
Next, apply the stain. The stain can be applied by spraying or brushing the stain onto one end of the furniture. Work slowly and carefully, moving back and forth along the grain of the wood until you reach the opposite end. Make sure that the stain does not drip off the edge of the wood. Let the stain dry completely before proceeding with the next steps.
To protect the painted surface, apply a coat of clear polyurethane sealant. Apply three coats with polyurethane. Allow the third coat of polyurethane sealer to dry overnight before applying the final coat.